Short description |
Drying of manure using external heat. For liquid manures, drying follows concentration by evaporation.
|
Best Available Technique: |
Not indicated |
Objective |
The aim of this treatment is to obtain a dried product from manure/slurry (solid fraction, raw or digested) with most of the nutrients, easier and cheaper to transport and land spreading. Depending of the moisture content of the product (slurry) a previous evaporation process is required.
|
Level of complexity |
|
Usual scale |
|
Innovation stage |
|
General diagram |
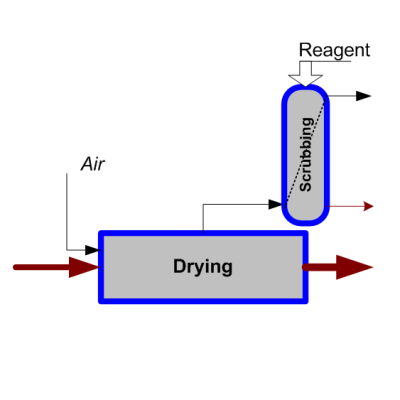
|
Applied to |
|
Typical technology combinations |
20+21 (with different combinations previous to drying (20)
|
Pictures |
|
Theroetical fundamentals and process description |
Water from previously centrifuged slurry and/or the concentrate of an evaporation process is removed (vaporized) applying heat. Thermal energy is usually recovered from a combined heat and power (CHP) engines or other heat residual streams.
The aim of the drying process is to obtain a product easily to handle, that conserve most of the nutrients of the original material (N:P:K). The dried product can be stored in a silo and transported pneumatically or by belt conveyor systems.
The gaseous emissions from the dryer must be recovered (by filtration or scrubbing) to avoid ammonia (NH3) or organic volatiles (VOC) emissions. If the product comes from anaerobic digestion process, this reduces VOC emissions, and the biogas produced covers part of the thermal energy needs (10-20%). Acidification of the input product, in order to control ammonia emissions, is also necessary.
When combined with nitrification-denitrification process, VOC and ammonia emission can be controlled, but poor nitrogen recovery is expected. If nitrification is applied but not denitrification, nitrogen recovery can be improved.
|
Environmental effects |
Effects on air (emissions):
- There is a potential risk of air pollutant emissions. Previous nitrification-denitrification process, acidification or anaerobic digestion and recovery of emissions from the drier (by filtration or scrubbing) to avoid ammonia (NH3) or organic volatiles (VOC) emissions are necessary to reduce such emissions.
- Maurer & Müller (2012) found ammonia-N losses of 77 and 91% during the drying of two types of dewatered digestate. The loss of total N for the two types were 63 and 70%, respectively, which indicates that losses of organic bound nitrogen was low. Almost all nitrogen in the dried products were organic bound. The feedstock of the biogas plant was a mixture of residues from food and feed production, pig, and cattle slurries as well as energy plants.
- The losses of nitrogen during drying can be reduced substantially by acidifying the input material. Pantelopoulos et al. (2016) found in line with Maurer & Müller (2012) that 95% of the NH4-N were lost following thermal drying of separation solids of digestate, whereas this loss was reduced to 27.2% and 17.1% by acidifying the material to pH 6.5 and 5.5 respectively.
- The C concentration of the material is significatly decreased as a result of the acidification. Pantelopoulos et al. (2016) found a C loss of 7% and 8% for separation solids of digestate that were acidifyed to pH 6.5 and 5.5 respectively. This corresponds to an organic matter loss of about 17.5-20%. The C losses during acidification is mostly related to the reaction of the strong acid with the solids’ carbonates and the subsequent CO2 emission.
Effects on water/soil (and management):
- Cu, Zn and other heavy metals are present in the dried product (depending of their concentration in the raw manures). This fact could limit their use on field crops.
- Need of special machinery for land spreading if pelletizing is not applied (dust product).
Other effects:
- Production of a dried product easily to handle, with moderate-high concentration of nutrient (N and P).
- Organic matter stabilization, pathogens and seeds removal. The dried product could be considered sterilized (according to the operation time/temperature).
|
Biosecurity aspects |
Not indicated |
Technical indicators |
Conversion efficiency:
High efficiency. More than 85% of the water is removed and 95% of the N (if previously acidified), and almost all P and K of the inflow could be conserved in the dried product.
Net energy consumption - explanation: High energy consumption (high temperature is required). For and industrial scale facility the thermal requirements can be estimated in 15-18 KW/m3 for S/L acidified-digested slurry entering at 25-30% TS. Subsidies (eg. to power production) are usually necessaries to make economical feasible these kind of treatment facilities.
Reagent 1 - explanation: No reagents. Sulphuric acid could be used in a previous acidification step to control NH3 emissions.
|
Observations |
- No specific equipment to dry slurries/manures is available. It is necessary to adapt equipment from other technologies (mainly animal feed production).
- It is of high relevance the selection of the constructive materials (resistance to high temperature and corrosion). It requires stainless steel quality >316L.
|
Economic indicators (Economic figures are rough indications, which cannot be used for individual project planning) |
Quantifiable income - text: The marked prices of the pellet from pig slurry (the dried product is usually pelletized) are between 30 and 55 €/t. If the dried product is not pelletized, its price is lower (25-30 €/t).
Non economically quantifiable benefits: Favours closing the nutrient cycle, consequently the consumption of fossil fuels used to synthesize chemical fertilizers is reduced. Transporting end-products nutrients concentrate to high distances .
|
Literature references |
- Bonmatí, A., Campos, E., Flotats, X. (2003). Concentration of pig slurry by evaporation: anaerobic digestion as the key process. Water Sci. Technol. 48: 189-194.
- Bonmatí, A., Flotats, X. (2003). Pig slurry concentration by vacuum evaporation: influence of previous mesophilic anaerobic digestion process. J. Air Waste Manage. Assoc. 53: 21-31.
- Burton, C.H., Turner, C. (Eds) (2003). Manure Management. Treatment strategies for sustainable agriculture. Silsoe Research Institute, 490 pps. ISBN: 0-9531282-6-1.
- Martens, W. Böhm, R. (2009). Overview of the ability of different treatment methods for liquid and solid manure to inactivate pathogens. Bioresource Technology, 100(22): 5374-5378.
- Maurer, C. and Müller, J. (2012), Ammonia (NH3) emissions during drying of untreated and dewatered biogas digestate in a hybrid waste-heat/solar dryer. Eng. Life Sci., 12: 321-326. https://doi.org/10.1002/elsc.201100113
- Pantelopoulos, A., J. Magid & L. Stoumann Jensen. 2016. Thermal drying of the solid fraction from biogas digestate: Effects of acidification, temperature and ventilation on nitrogen content. Waste Management 48 (2016) 218-226. https://doi.org/10.1016/j.wasman.2015.10.008
|
Real scale installation references |
- TRACJUSA and VAG (Juneda, Spain)
- SAVA (Miralcamp, Spain)
- VALPUREN-BAÑUELO/VALPUREN POLAN (Toledo, Spain)
|
Examples of suppliers |
Scolari. https://www.scolarisrl.com/ |